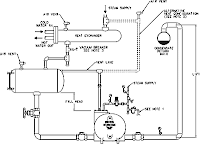 |
Recover/return steam condensate |
An often overlooked place to find savings in the operation of a manufacturing plant is the steam condensate return system. Returning condensate to the boiler feedwater system saves energy by returning pre-heated water, thus requiring less energy to maintain the feed water temperature. Furthermore, condensate is pre-treated, eliminating the need for additional expensive treatment.
Steam use in modern plants is everywhere. The condensate derived from its use is an asset that needs to be recycled. Older steam systems may have poor condensate return piping, or none at all. For these situations, creating or extending return lines should be considered. Steam traps in older systems are also suspect. Older traps are not as efficient or reliable as newer designs.
According to
Armstrong International’s Senior Utility Systems Engineer Novena Iordanova, steam traps are very important in the condensate return/feedwater cycle. She believes the first purpose of a steam system is to deliver steam to a users defined area of need, and second, to return the resulting condensate back to the boiler. Unfortunately, in many cases the second goal is overlooked.
In older plants, a
complete steam system evaluation, and many times an overhaul, is required. Professionals should be called in as plant maintenance staff typically doesn’t have the expertise required. The reasons for steam system degradation are common in the life cycle of plant operation. Over time, plant upgrades, new lines, expansion, and new equipment can have a significant detrimental effect on condensate return systems. The focus usually goes to the main headers and distribution, but condensate return doesn’t receive the same attention. The result can be a steam system that is no longer efficient - meaning high back pressures, water hammer, broken or freezing pipes, and leaks. At that point, the plant needs
professional help for a complete system review.
The most important player in condensate recovery is the steam trap. Steam traps play the critical role of separating steam and condensate at the moment its formed. Traps discharge the condensate downstream to the boiler for reuse. Proper sizing, installation, and maintenance from the start will save huge amounts of money in terms of energy savings and maintenance time.
Frequent and regular inspections of steam traps are essential, but in reality they are many times postponed or rescheduled. Steam trap inspection is tough work. Traps are usually located in hard to see, hot, and tight areas. Over time, the difficulty (combined with the perceived low priority) degenerates to spotty inspection routines, higher trap fail rates and higher steam costs.
The good news is that steam trap monitoring systems now exist that can monitor the performance of steam traps and alert maintenance when things start to deteriorate. Steam trap monitoring systems report conditions that point to filature, and also alarm when things break down. Accordingly, maintenance is in a position to take preventive action, or make swift repairs. Any plant with a considerable number of stream traps should strongly consider deploying a steam trap monitoring system.
Steam trap monitoring systems monitor the thermal and acoustic characteristic of the trap and report any significant changes. Today many monitoring systems are wireless, and many operate on common plant communication systems such as WirelessHART, a communication protocol gaining worldwide acceptance.
Its important to mention here though, the on the most common mistake plant personnel make when it comes to their system is also one of the most obvious - insulation. The use of high quality, well maintained insulation, installed to allow access to steam components is critical. The energy savings alone from well insulated pipes and traps is argument enough for making the initial time and dollar investment for proper insulating.
If you’re a plant manager and are looking for significant measurable and meaningful ways to lower energy costs, you must consider a
well planned and well executed steam trap management program.